Requirements
For this 2C injection molding flange, the ideas of reducing costs and the precision of the handling system were the focus of the process design. The automotive assembly is used in vehicle heating systems and ensures the transition from the heating element to the piping system. An insert nut is inserted into a multifunctional hybrid tool and overmolded in the 2C injection molding process.
A particular challenge here was the insert, which could not be pulled out of the component during assembly and so could not be overmolded. Due to the demanding materials, the processes had to be designed to be particularly stable and automated in order to avoid process fluctuations.
Process
All value-added steps were mapped at the Oelsnitz site in a holistic production process – from supporting the customer in product development and developing a manufacturing and automation concept through to building the system, including injection molding tool, vibratory bowl feeder, testing device, removal station and gripper system.
To increase the extraction force, a proposed modification to the bushing geometry was first introduced. It was possible to optimize the insert, originally designed as a cylinder with knurling, as a collar solution. This has the advantage that the collar can also be used as a stop collar in handling and at the pick-up station. This in turn allows significant cost savings to be generated as it is possible to implement a linear solution without other technologies.
A high-quality 2-component injection molding tool with an index panel makes it possible to manufacture in a mold and on a machine. Several work processes can run at the same time, e.g., overmolding the bushing with base body and the simultaneous molding of the seal at station 2. The electrical servo rotary drive ensures high accuracy at high speeds and low wear.
We use a robust PA6.6 GF30 for the base body, which has high strength and temperature resistance. The seal membrane consists of TPE, which features a hardness suitable to the stresses placed on it in use.
The handling head was designed in such a way that all linear movements can take place in the multifunctional gripper with pneumatic actuation units. Components are removed here; the semi-finished component is flipped over and the bushing inserted – a clear benefit as cost-intensive robot systems are not necessary. The design and layout of the vibratory bowl feeder are coordinated so that the bushings of bulk material are separated and arrive at the discharge station in the correct position. Thanks to automation in the process, a complete inspection can be carried out via inspection stations with optical and inductive sensors during removal. This means the presence of the bushing can be confirmed and possible overmolding of the thread can be identified in good time.
Result
Our customer benefits from the cost savings on the total order volume. The one-off investment at the start pays off here as the use of several production employees can be saved in the long term. In addition, scrap is reduced to a minimum. Possible sources of error can be detected by the 100% inspection and subsequent failures in the assembly can be prevented.
In terms of process efficiency, it also shows that the machines can run almost autonomously and that downtimes can be minimized thanks to the automatic ejection of defective parts. This, in turn, is associated with cost and energy savings as it is not necessary to lower or warm up the machines. At the same time, the rejection of plastic masses can be significantly reduced.
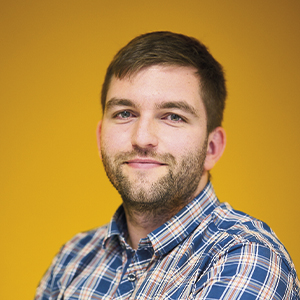
Personal contact
Markus Schwab
Are you interested in our industry solutions, would you like to convince yourself of our capabilities, or would you like to get a project off the ground?